Know What AND Know When
- Vaughn Mantor
- Oct 18, 2022
- 5 min read
Updated: Dec 14, 2022
10/18/2022 | Vaughn J. Mantor
The quarterback took the snap from the shotgun position. Three receivers ran their routes spot-on, and the second target came open. But the quarterback hesitated, only 2/10 second. Just enough time for the defensive back to cut in front of the receiver. The crowd roared for one of the most exciting plays in football: Interception for a touchdown.
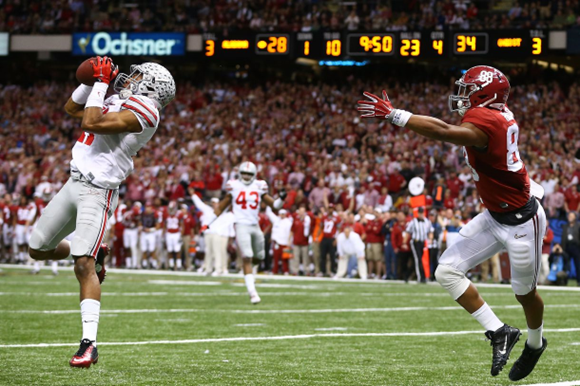
To state the obvious, a tiny error in “when” meant failure. Hesitation, procrastination, delay, dally, dawdle, and dither all conspire to steal success.
So, what’s the link between football and laser scanning technology? Poor timing can be costly.
Many construction projects include changes to existing structures. These projects get started when someone has a vision of what the structure could become. From that point on, every group involved in the project could save time and money if they had accurate, as-built information about the structure. And that’s where Verify 3D comes in.
We know not everyone who reads this article has experience with 3-dimensional laser scanning. So if you’re not yet familiar with the technology, we’ve put a summary at the end of this article.
Too often, laser scanning technology is classified as a subcontracting function, and our services have proven valuable whenever we’re called in, but waiting wastes time and money.
The sooner laser scanning is done, the better. The scanning data save time and money by giving architects, engineers, designers, contractors, and managers the information they need, exactly when they need it.
We’ve learned a few things in the past two decades in which we’ve worked with laser scanners. Here are a few examples from our files that illustrate this point for many types of construction.
First, changes to existing structures.
Example 1. A fish hatchery wanted to expand by 50%. But they did not have access to enough water to expand that much. Would it be feasible to bring water from behind a dam, from the penstocks, a few miles away? And, of course, the cost of pumping water that far would affect the resources available for the expansion of the hatchery itself. Early in the feasibility study, the engineers brought in Verify 3D to scan the penstocks, the prospective route for the water pipe, and the existing fish hatchery.

Above, a laser scan of a portion of the fish hatchery.
According to the engineer in charge, the laser scanning shaved three weeks from the project plan of just the feasibility study. They planned to use the data throughout the project and anticipated considerably more savings.
Example 2. Most of those in the construction trades recognize this sentence, “Contractor is responsible for verifying the accuracy of these drawings.” To accept that risk, contractors rightly increase their bids. But in Nashville, construction work has been so plentiful that contractors can pick the jobs they want to do. So the city and their advisors decided to laser scan the school buildings scheduled for modifications before starting the redesign.
Since Nashville has taken this approach, the risk of inaccurate drawings was reduced to nearly zero, and the contractors have submitted more accurate bids, and the number of RFIs was substantially reduced. Millions of dollars were saved.
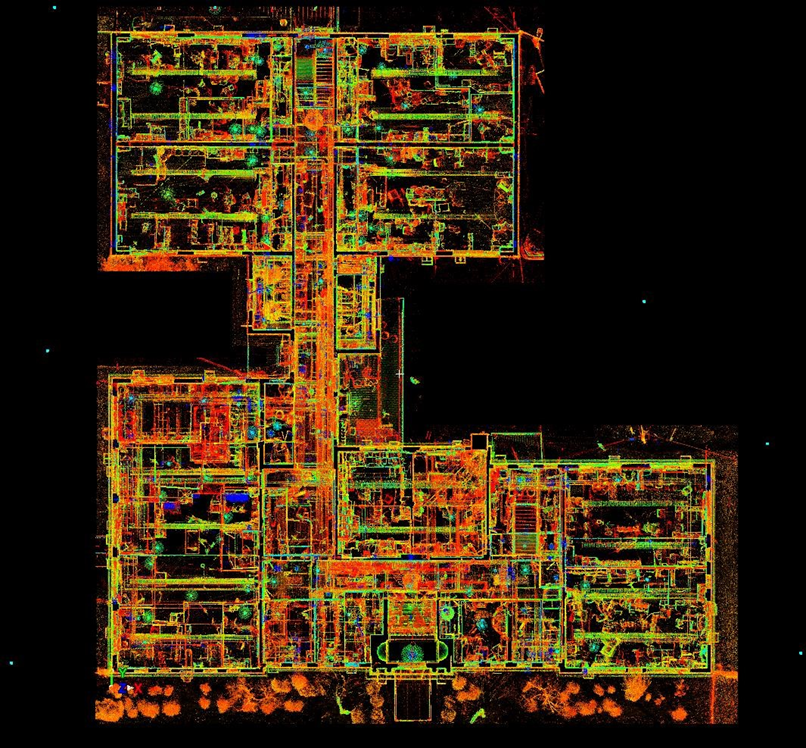
The image above is a transparent plan view of two stories of a school in Nashville. Every element, including lighting locations, piping, ductwork, fixtures, etc., is accurately measured. This image is shown in false color based on reflectivity, but by merely changing the parameters of the viewing software, the point cloud can show the flatness of flooring or the plumb of walls, et al.
Example 3. This just in. As we were preparing this article for publication, we received a new request for scanning and modeling. Paraphrasing the client, “We want to undertake important renovations for our 100 year-old building. But we don’t have a lot of money so we will prioritize the renovations depending on what the architects, designers, and engineers tell us is the price of each component of the renovation.” They asked for a scan and CAD model of the entire building. The architects, designers, and engineers could use the CAD model to estimate the price of each renovation.
We are advising them that we could save them time and money by a different approach: 1. Scan. 2. Combine the scans into a virtual, measured duplicate of the building (a complete point cloud), which would be accessible by anyone involved in the project. 3. Let the architects, designers, and engineers work with the virtual duplicate to fit the renovations into the budget. 4. Model the affected areas only, and with the minimum complexity necessary for those who will use the CAD model.
We can’t show you the building involved; we’re still writing the proposal, but you can see an example of a virtual, measured duplicate in a video here.
Second, scanning earlier also applies to new construction.
Example 4. The Detroit Zoo chose Albert Kahn Associates to design a new, $26,000,000 home for the waddle of penguins in the zoo’s care. (Waddle is a group name for penguins, and seems appropriate.) The architect specified laser scanning at crucial points in the project, in part because the shape of the building is irregular, much like an iceberg.

Above, the completed Polk Penguin Conservancy at the Detroit Zoo.
Even before the structural framework was complete, laser scanning revealed that sections of the tubular steel frame were welded in place upside down and backwards. Without laser scanning, the errors would not have been discovered until much later in the project. The laser scanning saved several times the cost of the scanning.
Talk with us at the earliest point in your project, when you first contact the architect. If laser scanning makes any sense for your project, we’ll advise you of the best times for scanning and a draft of the scanning specifications that will save you the most time and money.
We don’t charge for this service.
If you’d like a personal exploration or demonstration of the ways laser scanning can help you, or if you’d like to speak with one of our clients, see our contact information below.
Because our experience in this technology dates to 2002, Verify 3D knows the most appropriate equipment to use on each project and how to use it for the best benefit to our clients. Much of the time, we use a Leica P-30 laser scanner, Leica Cyclone software for registration, and Revit for CAD modeling, but not exclusively. We use other makes and models of scanners, registration software, and CAD models.
How laser scanning (also called LiDAR) works
The laser scanner is a device about the size of my head. We put it on a tripod, adjust the settings, and the machine shoots 1,000,000 laser beams per second, in a controlled pattern 360º horizontally 300º vertically. Each beam reflects off something and comes back to the scanner, and as it returns to the device, the scanner computes X, Y, & Z coordinates for the spot the beam reflected from. In a couple minutes, we collect over 100 million accurate 3D measurements. Then we move the scanner to a new position nearby to scan objects not visible from the earlier position (The laser beams are weak, they penetrate nothing, not even paper.). We repeat the scanning in as many places as needed for the project. The specific numbers in this paragraph are based on the specifications of a Leica P30. Other models and makes will have different specifications, but the basics are the same.
We collect all the data from all the scanning positions into a single coordinate system chosen by the client. A single coordinate system means everyone uses the same set of measurements. From this base set of data, we create many different types of drawings and diagrams. An abbreviated list includes 2D & 3D CAD models in many formats, all manner of 2D drawings, videos, deviation diagrams, topographic maps, and many more. We can even show how objects move over time.
Comments